Using 6/3 Aluminum Wire for a Range: A Comprehensive Guide
When installing a new electric range or upgrading an existing one, selecting the appropriate wire size and type is crucial for safety and performance. One commonly used wire for this purpose is the 6/3 aluminum wire.
Understanding its specifications, applications, and installation requirements ensures that your range operates safely and efficiently. This article provides an in-depth look at using 6/3 aluminum wire for ranges, covering key aspects from wire properties and safety considerations to installation guidelines and compliance with electrical codes.
You'll Learn About
Understanding 6/3 Aluminum Wire
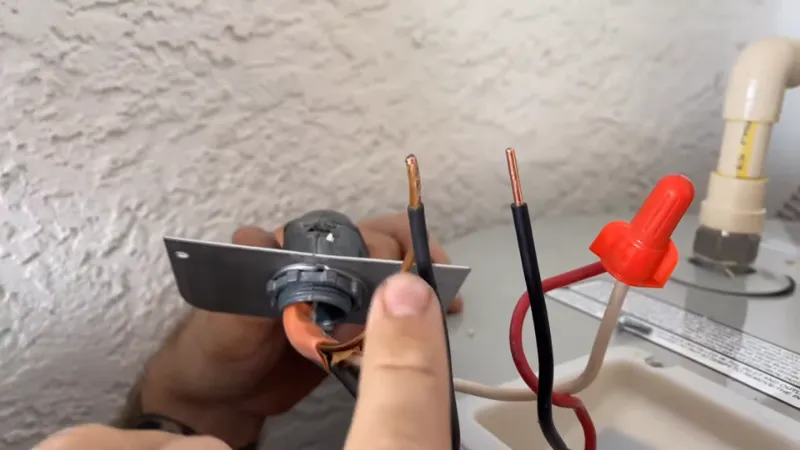
What is 6/3 Aluminum Wire?
6/3 aluminum wire consists of three conductors, each with a 6-gauge diameter, and an additional ground wire. The “6” denotes the gauge of the conductors, and the “3” indicates there are three insulated conductors. Aluminum wiring is often used as an alternative to copper due to its cost-effectiveness and satisfactory performance in specific applications. Some appliences doesn’t have grounds.
Properties of Aluminum Wire
- Conductivity: Aluminum has about 61% of the conductivity of copper, requiring larger gauges to carry the same current.
- Weight: Aluminum is lighter than copper, making it easier to handle and install.
- Cost: Aluminum wire is generally less expensive than copper, making it a popular choice for budget-conscious projects.
- Corrosion Resistance: Aluminum naturally forms an oxide layer that resists corrosion, but connections must be carefully managed to prevent oxidation that can cause resistance and heat.
Applications of 6/3 Aluminum Wire
- Electric Ranges: Suitable for powering electric ranges that require a 50-amp circuit.
- Large Appliances: Can be used for other large appliances such as ovens and dryers, where appropriate.
- Subpanels: Sometimes used to connect subpanels in residential wiring.
Safety Considerations
Code Compliance
Ensuring compliance with the National Electrical Code (NEC) and local building codes is critical. The NEC provides guidelines for wire size, installation methods, and safety practices.
- NEC Guidelines: According to the NEC, 6/3 aluminum wire is suitable for a 50-amp circuit, which is typically required for electric ranges.
- Local Codes: Always check local building codes, as they may have additional requirements or restrictions.
Connection and Termination
Proper connection and termination of aluminum wire are essential to prevent electrical hazards.
- Anti-Oxidant Compound: Use anti-oxidant compound on aluminum wire connections to prevent oxidation and ensure a secure connection.
- Appropriate Connectors: Use connectors rated for aluminum wire, such as AL/CU (aluminum/copper) rated connectors, to prevent galvanic corrosion.
Handling and Installation
Careful handling and installation are necessary to avoid damaging the wire.
- Avoid Kinks and Bends: Aluminum wire is more prone to breaking if repeatedly bent or kinked. Handle the wire carefully to maintain its integrity.
- Proper Support: Support the wire adequately to prevent sagging and mechanical stress.
Installation Guidelines
Tools and Materials Needed
- 6/3 Aluminum Wire
- Wire Cutters
- Wire Strippers
- Anti-Oxidant Compound
- AL/CU Rated Connectors
- Screwdrivers
- Electrical Tape
- Conduit (if required by code)
Step-by-Step Installation
Planning and Preparation
- Determine Circuit Requirements: Verify the amperage requirements of your electric range. Most ranges require a 50-amp circuit, which is suitable for 6/3 aluminum wire.
- Turn Off Power: Before starting any electrical work, turn off power to the circuit at the main breaker panel.
- Measure and Cut Wire: Measure the distance from the breaker panel to the range location and cut the wire to the required length, allowing extra for connections.
Running the Wire
- Route the Wire: Run the 6/3 aluminum wire from the breaker panel to the range location, following the shortest and most practical path.
- Conduit Use: If local codes require, run the wire through appropriate conduit. Secure the conduit to walls and ceilings as needed.
- Drilling Holes: If running the wire through walls or floors, drill appropriate holes to accommodate the wire. Ensure holes are smooth to prevent damage to the wire insulation.
Connecting to the Breaker Panel
- Strip Insulation: Carefully strip the insulation from the ends of the wire using wire strippers, exposing about 3/4 inch of the conductors.
- Apply Anti-Oxidant Compound: Apply anti-oxidant compound to the exposed aluminum conductors to prevent oxidation.
- Connect to Breaker: Connect the black and red wires (hot wires) to a double-pole 50-amp breaker. Connect the white wire (neutral) to the neutral bus bar and the bare or green wire (ground) to the ground bus bar.
- Secure Connections: Tighten all connections securely, ensuring there is no loose wiring.
Connecting to the Range Outlet
- Install Outlet Box: Install an appropriate outlet box at the range location if not already present.
- Wire the Outlet: Connect the wires to the range outlet terminals following the manufacturer’s instructions. Typically, black and red wires go to the hot terminals, white to the neutral terminal, and bare or green to the ground terminal.
- Secure the Outlet: Secure the outlet to the box and attach the cover plate.
Final Checks and Power Restoration
- Inspect All Connections: Double-check all connections for security and correctness.
- Restore Power: Turn the power back on at the main breaker panel.
- Test the Circuit: Test the range to ensure it is operating correctly.
Troubleshooting and Maintenance
Common Issues
- Loose Connections: Can cause overheating and potential fire hazards. Regularly inspect connections to ensure they are tight.
- Oxidation: Aluminum wire can oxidize over time. Apply anti-oxidant compound during installation and check periodically.
- Overloading: Ensure the range’s electrical requirements match the circuit rating to prevent overloading.
Maintenance Tips
- Regular Inspections: Periodically inspect the wiring and connections for signs of wear, corrosion, or damage.
- Professional Inspections: Have a licensed electrician inspect the installation if you notice any issues or during routine home maintenance checks.
What size aluminum wire will carry 50 amps?
Before we delve into the specific wire size for carrying 50 amps, let’s clarify some fundamental concepts:
- Wire Gauge: This refers to the thickness of a wire, measured in American Wire Gauge (AWG). A lower gauge number indicates a thicker wire, which can handle higher current.
- Ampacity: This term represents the maximum amount of current that a wire can safely carry without overheating. It is influenced by factors like wire material, insulation type, ambient temperature, and installation method.
Choosing the Right Wire Size for 50 Amps
According to the National Electrical Code (NEC), the recommended wire size for a 50-amp circuit is:
- 4 AWG aluminum wire
- 6 AWG copper wire
Why Aluminum Over Copper for 50 Amps?
While copper is a popular choice for wiring due to its excellent conductivity, aluminum has some advantages in certain applications:
- Cost-Effectiveness: Aluminum is generally more affordable than copper, making it a budget-friendly option for larger-gauge wires.
- Lower Weight: Aluminum is lighter than copper, which can be beneficial in long runs or installations where weight is a concern.
- Similar Ampacity: In many cases, aluminum wire can handle the same amperage as copper wire of a similar gauge.
However, it’s important to note that aluminum wire has some drawbacks:
- Oxidation: Aluminum is prone to oxidation, which can lead to increased resistance and potential overheating if not properly installed and maintained.
- Installation Requirements: Aluminum wire requires specific installation techniques and connectors to ensure a reliable connection.
Factors Affecting Wire Size Selection
In addition to the desired ampacity, several other factors influence the choice of wire size:
- Voltage: Higher voltage requires thicker wires to handle the increased electrical potential.
- Circuit Length: Longer runs of wire will experience greater voltage drop, necessitating larger wire sizes to compensate.
- Ambient Temperature: High temperatures can reduce the ampacity of wires, so it’s important to consider the installation environment.
- Installation Method: The method of installation, whether in conduit or direct burial, can affect the wire’s ampacity.
Consulting a Qualified Electrician
It’s crucial to consult with a qualified electrician to determine the appropriate wire size for your specific application. They will consider factors such as the load requirements, circuit length, and local electrical codes to ensure a safe and reliable installation.
Additional Considerations
- Circuit Breaker: Ensure that the circuit breaker is rated for the correct amperage (50 amps in this case) to protect the circuit from overload.
- Connectors and Terminations: Use connectors and termination methods specifically designed for aluminum wire to prevent corrosion and ensure a secure connection.
- Regular Inspection: Periodically inspect aluminum wire installations to check for signs of oxidation or loose connections.
Key Specifications and Considerations
Specification | Details |
---|---|
Wire Gauge | 6 AWG (American Wire Gauge) |
Number of Conductors | Three conductors plus a ground wire (6/3) |
Material | Aluminum |
Ampacity | Rated for 50 amps |
Common Applications | Electric ranges, large appliances, subpanels |
Code Compliance | Must comply with NEC and local building codes |
Connection Requirements | Use AL/CU rated connectors and anti-oxidant compound to prevent corrosion |
Installation Notes | Handle carefully to avoid kinks and ensure proper support |
Safety Measures | Turn off power before installation, use proper tools, and follow all safety guidelines |
Conclusion
Using 6/3 aluminum wire for an electric range is a cost-effective and practical solution, provided that proper installation techniques and safety measures are followed. Ensuring compliance with the NEC and local building codes, using the appropriate connectors and anti-oxidant compound, and handling the wire with care are all crucial steps in the installation process. By following this comprehensive guide, homeowners can confidently install 6/3 aluminum wire for their electric range, ensuring a safe and reliable electrical connection that meets all regulatory standards.