Is a Butt Edge to Tapered Edge Drywall Joint OK? An In-Depth Guide
Drywall installation involves many technical aspects, and one common question homeowners and contractors have is whether a butt edge to tapered edge drywall joint is acceptable. While technically possible, professionals generally prefer a tapered edge to tapered edge joint because it ensures smoother finishes and fewer problems over time. This blog will explore the differences between these joint types, when a butt to tapered edge joint might be necessary, and how to make it work effectively.
Understanding these technical choices will give you insight into professional drywall practices and ensure that your drywall project achieves a professional finish every time. Read on to discover the pros, cons, and best practices for each joint type.
You'll Learn About
Understanding Butt and Tapered Edges in Drywall
Before diving into the technicalities of joining these edges, let’s first define what a butt edge and tapered edge are in drywall terminology. These are two common types of drywall edge configurations used during installation.
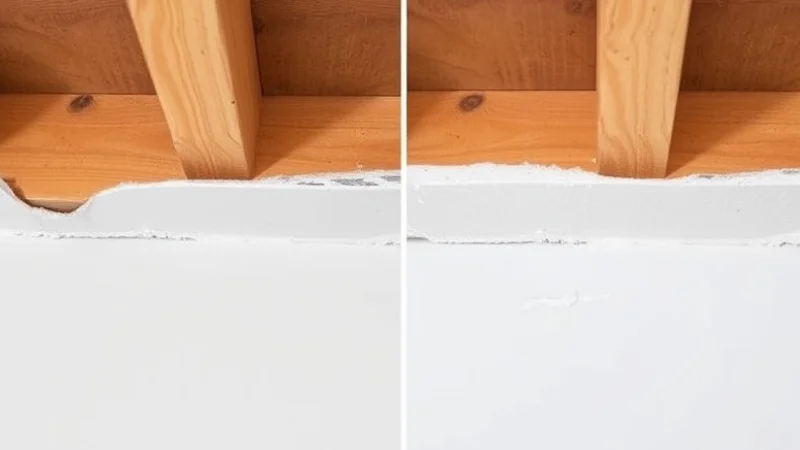
What is a Butt Edge?
A butt edge refers to the square, flat edge of a drywall panel. This type of edge meets another panel at a 90-degree angle, creating a “butt joint.” Butt edges are often easier to work with but can lead to visible seams if not managed properly.
What is a Tapered Edge?
A tapered edge is a beveled or angled edge on a drywall panel. It creates a shallow “V” shape when two panels meet, allowing joint compound to fill in the gap more smoothly. This creates an almost invisible joint once properly finished.
Why Do These Edge Types Matter?
The choice between butt and tapered edges directly affects how well a drywall seam can be finished. The design and type of joint determine the overall appearance of the final wall or ceiling surface.
Why Do Professionals Prefer Tapered Edge to Tapered Edge Joints?
When installing drywall, most professionals recommend a tapered edge to tapered edge joint instead of a butt edge to tapered edge joint. This preference comes with several benefits related to appearance, longevity, and ease of application.
Smoother Finish with Tapered Edges
The main reason tapered edge to tapered edge joints are preferred is because they create a much smoother finish. The “V” shape allows for joint compound to fill evenly, minimizing the appearance of seams and creating a seamless look.
Less Chance of Cracking
Tapered edges reduce the risk of cracking over time compared to butt joints. With butt joints, the gap between panels is larger, increasing the likelihood that cracks will develop if the joint compound isn’t applied evenly.
More Efficient Joint Compound Application
The “V” shape created by tapered edges allows for better joint compound application. The compound easily adheres to the angled surface, ensuring a strong bond and better overall coverage.
Enhanced Aesthetic Appeal
Tapered joints look far better aesthetically because they create a seamless finish, while butt joints tend to be more noticeable. Many professional projects require this clean, professional look to meet client expectations.
When is a Butt Edge to Tapered Edge Joint Necessary?
Although tapered edge to tapered edge joints are preferred, there are instances when a butt edge to tapered edge joint becomes necessary. Understanding when to make this choice will save time, prevent frustration, and lead to better results.
Limited Space Situations
In tight spaces or tricky installation areas, aligning a tapered edge joint might be physically difficult. A butt edge to tapered edge joint may provide the only practical solution in these situations.
Repairing Existing Drywall Damage
If you are patching or repairing drywall, you may encounter situations where one edge is already tapered and the other is a butt edge. A butt to tapered joint becomes necessary in these cases to maintain structural integrity and aesthetics.
Older Drywall Installations
Some older homes or projects may feature existing butt edges that must be worked with during renovations or repairs. In these cases, creating a butt edge to tapered edge joint allows for a functional repair without tearing out large sections of drywall.
How to Properly Create a Butt Edge to Tapered Edge Drywall Joint
When you must use a butt edge to tapered edge joint, following proper techniques ensures that the final result is smooth and long-lasting. Here’s how you can achieve a successful joint using the correct tools, materials, and techniques.
Step 1: Apply a Generous Amount of Joint Compound
When creating a butt edge to tapered edge joint, apply a generous amount of joint compound over the butt edge. This will fill the gap between the two edges and provide a solid foundation for the tape and finishing layers.
Step 2: Use Quality Drywall Tape
Select a high-quality drywall tape designed for wide-gap application. Properly embedding the tape into the joint compound ensures a strong, seamless bond and prevents future cracking.
Step 3: Apply Multiple Coats
One coat of joint compound is rarely enough to achieve a smooth finish with a butt edge to tapered edge joint. Allow the compound to dry completely between coats, and apply two to three thin layers for best results.
Step 4: Smooth Out the Compound
After applying joint compound and tape, smooth the surface with a drywall knife. Use long, even strokes to spread the compound evenly over the seam while removing excess.
Step 5: Sand Between Coats
Once the joint compound has dried completely, lightly sand the surface with fine-grit sandpaper. Sanding between coats ensures a seamless and smooth surface before applying additional coats.
Common Mistakes to Avoid with Butt Edge to Tapered Edge Joints
Even the most experienced DIYers and contractors can make mistakes when creating these joints. Avoiding common errors ensures a professional finish and prevents future issues.
Mistake 1: Not Applying Enough Joint Compound
Failing to apply a generous amount of joint compound can leave uneven gaps, making the joint more likely to crack over time. Always fill the gap completely.
Mistake 2: Using Low-Quality Drywall Tape
Low-quality tape can lead to joint failure and cracking. Use durable, high-quality tape designed for wide-gap applications.
Mistake 3: Skipping Proper Sanding Between Coats
Skipping the sanding step between coats creates uneven surfaces and leaves behind visible imperfections. Always sand to ensure the surface is smooth and even.
Why Is Drywall Not Tapered on All Sides?
Understanding the Drywall Tapered Edge Design
Drywall is designed with tapered edges to make installation easier and smoother. These tapered edges are typically found on the long sides of drywall panels. The tapered design allows joint compound to be applied evenly for seamless seams between sheets.
However, drywall isn’t tapered on all four sides for practical reasons. Creating tapered edges on all four sides would increase production costs and complexity. Manufacturers focus on tapering only the long edges to keep costs lower without compromising function.
Tapered edges allow for better blending with joint compounds and fewer visible seams. This design is practical and efficient for most installation needs without raising costs. Drywall panels are designed to save time and resources while maintaining quality and ease of use.
Production Costs Would Increase with Four-Tapered Sides
Drywall is manufactured in continuous sheets that are cut to standard lengths. Common lengths include 8 feet, 10 feet, or 12 feet, and they are produced in an assembly line process. This efficient method keeps costs low and production high.
Adding tapered edges on all four sides would make production far more expensive. Manufacturers would need to implement additional machinery and processes to produce four tapered edges on every sheet. This would likely drive up the cost of drywall for consumers and contractors alike.
Drywall is meant to be affordable and accessible for construction projects. Avoiding additional costs by tapering only the necessary edges is a smart manufacturing decision. The trade-off allows drywall to remain cost-effective while maintaining its intended purpose.
How Drywall Tapering Saves Time and Labor Costs
Tapered edges are primarily placed on the long sides of drywall panels. These tapered sides allow for smoother joints when applying compound to the seams. They make it easier to blend and create a finished surface without visible ridges.
Because only the long edges are tapered, installation remains quick and efficient. If all four sides were tapered, additional labor would be needed to match and align the edges during installation. Contractors benefit from this streamlined approach, saving time and reducing labor expenses.
Installing drywall is already a time-consuming task, and minimizing unnecessary complexity is important. Drywall’s design allows workers to focus on installing the sheets without worrying about uneven or difficult seams. Keeping costs low while simplifying the installation process ensures contractors can maintain profitability.
The Role of Non-Tapered Edges in Drywall Installation
Non-tapered edges are located on the shorter sides of the drywall panels. These flat edges still allow drywall to be installed securely while minimizing waste. They can be used for areas where tapering isn’t required, such as in corner joints.
When installing drywall, non-tapered edges are often joined using additional joint compound or trim pieces. These methods provide durability and maintain an even finish without requiring the higher cost of full tapering. Drywall systems are designed with flexibility in mind, allowing for multiple installation methods.
Drywall construction has maintained its affordability by focusing tapering on just the long edges. Non-tapered edges are still functional and allow for efficient installations without unnecessary costs. This is a design choice that balances functionality with affordability for contractors and homeowners.
Why Drywall Keeps Costs Low for Common Use
Drywall is used in countless residential and commercial construction projects. Keeping costs low is essential to meet the demands of the construction industry. Most drywall is affordable because of its efficient manufacturing process, limited tapering, and standard production practices.
If all four sides of every drywall panel were tapered, costs would rise significantly. More specialized machinery would be required to create four tapered sides, leading to higher production costs. Most projects can still use tapered long edges effectively without requiring unnecessary tapering everywhere.
Drywall panels are versatile and cost-effective because they are designed to meet standard construction needs. Although not every edge is tapered, drywall remains easy to install and fits into a variety of environments. Keeping costs down allows drywall to be accessible for projects of all sizes.
Alternatives for Non-Tapered Edge Applications
For areas where a seamless look is important, other methods can be used. Corner trims, joint compounds, or specialized edge treatments can be applied where non-tapered edges are exposed. These solutions ensure that the finished project has a clean and professional appearance.
Trim pieces can be used to hide non-tapered edges and provide structural stability. These trims can be easily added during the installation process without requiring the full cost of tapering all edges. They are practical and effective solutions for areas that would otherwise require added attention.
Drywall remains versatile, and its design allows for alternative solutions when necessary. The combination of tapering on long sides and using additional tools ensures a seamless finish. Drywall installers can achieve smooth finishes without increasing costs by using strategic techniques for non-tapered edges.
Balancing Costs, Efficiency, and Practicality
Drywall’s design decisions are based on balancing affordability, ease of installation, and functionality. Tapering is focused on the long sides of the panel, allowing for a smooth installation without additional costs. Avoiding tapering on all four sides keeps the costs manageable for contractors and builders.
Every decision in drywall manufacturing is made with affordability and practicality in mind. By tapering only the necessary areas, manufacturers can keep the cost low while meeting the needs of most residential and commercial projects. Non-tapered edges are still functional and can be easily adjusted if needed.
Drywall remains one of the most cost-effective and efficient materials for construction. Every detail of its design reflects careful planning to ensure the needs of builders and homeowners are met. Keeping materials affordable without sacrificing performance has been key to drywall’s success for decades.
FAQs: Butt Edge to Tapered Edge Joint Questions
1. Can butt edge to tapered edge joints crack over time?
Yes, butt joints are more likely to crack over time because of uneven compound gaps.
2. How can I prevent cracking in butt edge to tapered edge joints?
Apply a generous amount of joint compound and use quality tape.
3. When would I need a butt edge to tapered edge joint?
In tight spaces, patchwork, or when replacing damaged drywall sections.
Conclusion: Should You Use a Butt Edge to Tapered Edge Joint?
While a tapered edge to tapered edge joint is the preferred method, butt edge to tapered edge joints are completely acceptable in certain circumstances. Proper application, high-quality materials, and attention to technique can make a butt edge to tapered edge joint effective and long-lasting.
Whether you’re a DIY enthusiast or hiring a professional, understanding the differences and when to use these methods will ensure that your drywall project has a smooth, professional finish. Choose the right method, and your walls and ceilings will look great for years to come!
A butt edge to tapered edge drywall joint can work with proper taping and mudding. For more drywall tips, check out our guides on 3/8 vs 1/2 drywall and plaster weld alternatives. If you’re tackling other home improvements, like running wire through a top plate, proper planning ensures a smooth finish.