How to MIG Weld Cold Rolled Steel: Tips, Techniques, and Best Practices
MIG welding cold rolled steel is a versatile and efficient process for creating strong welds. Cold rolled steel has specific properties that make it an excellent choice for structural projects. Understanding MIG welding techniques, settings, and common concerns ensures a high-quality weld with minimal rework.
By learning the nuances of working with cold rolled steel, you can optimize your MIG welding results. This comprehensive guide explores everything you need to know about welding cold rolled steel using Metal Inert Gas (MIG) welding methods.
You'll Learn About
Understanding Cold Rolled Steel: What Makes It Unique?
Cold rolled steel is a type of steel that has been processed after hot rolling. This processing creates tighter tolerances, a smoother surface finish, and superior mechanical properties compared to hot-rolled steel. These unique properties make it widely used in industries like automotive, construction, and manufacturing.
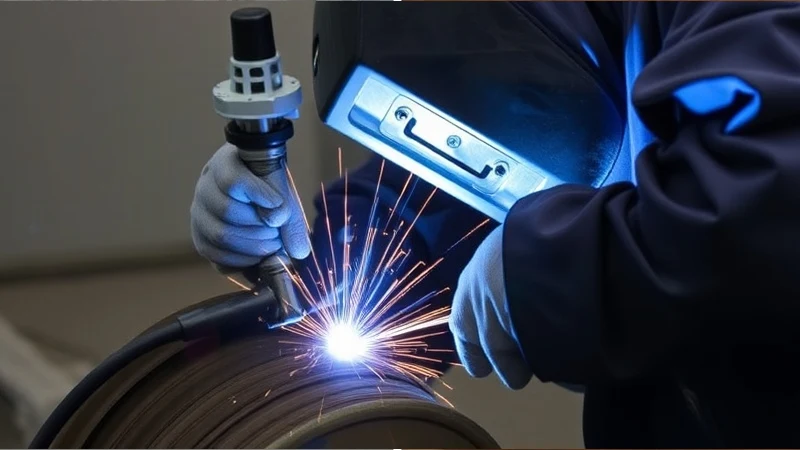
What is Cold Rolled Steel?
Cold rolled steel is created by further processing hot rolled steel at room temperature. This prevents the steel from expanding, resulting in increased strength and better surface characteristics. Cold rolled steel is easier to weld when proper preparation is followed.
Common Types of Cold Rolled Steel:
- CRS (Cold Rolled Steel) sheet: Thin sheets commonly used for light gauge applications.
- High-strength low-alloy steels (HSLA): Offer superior strength while maintaining ductility.
- Galvanized cold rolled steel: Zinc-coated to improve corrosion resistance.
Cold rolled steel is a great choice for projects requiring precision and strength. Understanding its properties is essential when welding.
Why MIG Welding Works Well with Cold Rolled Steel
MIG welding is one of the most popular welding techniques for cold rolled steel. It uses a continuous wire feed and shielding gas to produce a smooth, strong, and clean weld. MIG welding is faster and easier to control compared to other welding methods.
Key reasons MIG welding is ideal for cold rolled steel:
- Consistent weld quality
- Adjustable heat for precision
- Easy to learn for beginners
- Minimal cleanup required
Using the proper MIG welding technique ensures a successful result every time.
Preparing to MIG Weld Cold Rolled Steel
Before starting your MIG welding project, preparation is critical. Proper cleaning, selecting the right filler wire, and setting up the shielding gas are all vital steps to achieve clean, solid welds. Failure to prepare properly can lead to weak welds, contamination, or poor penetration.
1. Cleaning the Surface Thoroughly
Cold rolled steel has a smooth surface, which can hinder weld penetration. Cleaning removes any dirt, grease, oils, or mill scale that can prevent the MIG wire from adhering properly.
Cleaning Methods:
- Wire Brush: Removes visible contaminants and rust.
- Solvent Cleaning: Removes oil or grease using degreasers.
- Sandblasting: Suitable for larger projects to ensure all contaminants are removed.
A clean surface ensures that the weld penetrates the material correctly, creating a strong bond.
2. Choosing the Right Filler Wire
The selection of a compatible filler wire is crucial when welding cold rolled steel. A standard mild steel MIG welding wire works well for most applications.
Popular Filler Wire Options:
- ER70S-6: Suitable for general-purpose welding, offers good versatility.
- ER70S-3: Ideal for smooth welding without much spatter.
- Solid Wire vs. Flux Core Wire: Choose solid wires for clean welds or flux core for outdoor applications.
Selecting the appropriate wire ensures you’ll achieve strong, defect-free welds.
3. Selecting the Right Shielding Gas
Shielding gas protects the weld pool from oxygen and other contaminants. A gas mixture is required for optimal performance when welding cold rolled steel.
Common Shielding Gas Mixtures:
- 75% Argon / 25% CO2: The most popular combination for cold rolled steel.
- 100% Argon: Offers excellent weld quality, though it’s less common for cold rolled steel.
- Helium mixtures: Often used for thicker materials or specific applications.
Using the right shielding gas ensures minimal oxidation and excellent weld quality.
4. Heat Control and Welding Parameters
Cold rolled steel can warp or distort if exposed to too much heat. Managing voltage, amperage, and wire feed speed is key to avoiding excessive heat input and ensuring even welds.
Key MIG Welding Parameters:
- Wire Feed Speed: Adjust to ensure smooth wire delivery and steady welds.
- Voltage Settings: Match these to the material thickness for proper penetration.
- Amperage: Use the right amount to avoid burning through thin steel.
Maintaining proper heat balance allows for clean welds and prevents warping.
Common Concerns When MIG Welding Cold Rolled Steel
Understanding potential issues that arise when MIG welding cold rolled steel helps you troubleshoot and create better welds. These common concerns require attention during preparation and execution.
Work Hardening: What You Need to Know
Cold rolled steel can work harden in the weld zone, which means it becomes harder but more brittle under certain conditions. This can lead to cracks or premature failure if not addressed.
How to Avoid Work Hardening:
- Control heat input by fine-tuning your MIG settings.
- Use proper welding techniques to reduce stress.
- Avoid over-welding thin areas.
Work hardening must be minimized to ensure welds maintain their strength and flexibility.
Zinc Coating Problems
Some cold rolled steel has zinc coatings, which protect the steel from corrosion but can create hazards during welding. When exposed to heat, zinc can vaporize, creating toxic fumes.
Mitigation Strategies:
- Remove zinc coating from the weld area with sanding or grinding.
- Use adequate ventilation or a respirator to minimize exposure.
- Switch to specialized MIG settings if welding zinc-coated steel.
Taking proper precautions ensures the health and safety of the welder.
Troubleshooting MIG Welding Issues with Cold Rolled Steel
Even experienced welders can run into issues. Understanding common problems and their solutions can save time and frustration.
1. Spatter or Porosity in the Weld
Excess spatter can occur due to incorrect shielding gas, poor wire feed speed, or improper technique.
How to Fix:
- Adjust the shielding gas mixture.
- Fine-tune wire feed speed.
- Ensure surface cleaning is adequate.
2. Lack of Penetration
Poor penetration is often caused by insufficient heat input, incorrect settings, or dirty surfaces.
Solution:
Increase amperage or voltage while inspecting connections and cleanliness.
FAQs About MIG Welding Cold Rolled Steel
Q: Can I MIG weld cold rolled steel without preparation?
A: No, thorough cleaning is essential for optimal weld quality.
Q: Which shielding gas is the best for cold rolled steel?
A: A mix of 75% Argon and 25% CO2 is the most effective.
Q: How do I prevent distortion when MIG welding?
A: Adjust voltage, wire speed, and maintain consistent, controlled heat.
Final Thoughts
MIG welding cold rolled steel is an efficient and versatile process when approached correctly. Preparation, filler wire choice, shielding gas, and proper heat management are key factors for success. Whether you’re a seasoned welder or just starting, following these tips will ensure a clean, strong weld.
With proper practice and preparation, you can confidently MIG weld cold rolled steel with ease. Master these techniques and handle challenges effectively to achieve professional-grade results.
MIG welding cold-rolled steel requires proper technique and equipment. For more welding tips, explore our articles on how to straighten an aluminum plate and why mirrors are rusting. If you’re tackling other projects, like running wires through a brick fireplace, proper planning ensures durability.