What is the Acceptable Micron Rise? Everything You Need to Know
The level of vacuum in a refrigeration system is critical for its efficiency and longevity. Various standards exist to guide technicians on the best micron levels for evacuation.
However, some degree of micron rise during operation may be acceptable depending on the circumstances.
You'll Learn About
Ashrae Recommendations
The American Society of Heating, Refrigerating, and Air-Conditioning Engineers (ASHRAE) is a standards-setting organization for the HVAC industry. One of the topics they cover is evacuation, which is the act of removing air and moisture from a refrigeration or air conditioning system.
1000 Microns to Remove Moisture
In order to remove any moisture existing in the system, ASHRAE recommends emptying systems to below 1000 microns. Moisture can cause corrosion, resulting in leaks or compressor failure.
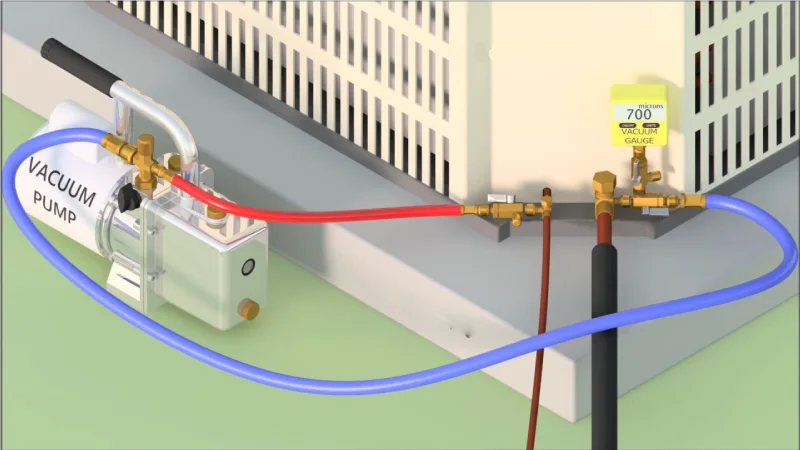
When temperatures dip too low, it can also freeze inside pipes, obstructing the flow of refrigerant and inflicting severe damage.
By evacuating a system down to such a low-pressure level, it allows any remaining water vapor within it to boil away at room temperature. That is, instead of freezing, it turns into ice when exposed to cold temperatures.
The cold is caused by either access humidity leaking in time or extensive installation mistakes. The error that may be created during the assembly process, such as loose connections, etc.
Evacuating beyond this stage would be ineffective since there would be insufficient molecules left behind. So boi, but I’d rather squander energy resources while exposing metal bits within the coils of the equipment.
It results in a shortened life duration, which is characteristic of acid development on these coil metal surfaces. Furthermore, having early indicators of degradation shortens their environmental usefulness cycle.
Evacuation Below 500 Microns After Replacing a Compressor
Inside heating ventilating air-conditioning controlled space environment after replacing a failed compressor unit with another. You can do it once all components have been thoroughly tested prior to installation; some manufacturers may specify further regulation levels.
They should require technicians to evacuate vacuum pumps with rated suction delivery capacity at acceptable charge head pressures. The reading is generally between the kiloPa units domain [20-kilopascal minimum needs] and high limits.
Also, depending on the individual model, potentially fifty kPa. Model variations with various range values are mandated in accordance with manual instructions provided with the replaced device machinery.
Some manufacturers still specify evacuation pressures as low as 400 microns. This is due to the possibility of water vapor and other contaminants during repairs or service failures during the compressor replacement procedure.
Otherwise, an electric equipment breaker tripped, resulting in a total functional shutdown of ready/standby operational capability. It is frequently encountered in large manufacturing factories that manufacture compressor-optimized circuits.
It must be removed from your system to ensure optimal functionality.
Two pressure levels are recommended by ASHRAE for evacuated systems. Lower than 1000 microns for moisture removal and lower than 500 microns after changing compressor types.
The operational circumstances that provide cooling effects aid in the removal of residual atmospheric gases such as air pollution, which reduces corrosive properties.
When such traits are present at interfaces between distinct tube networks, it is associated with acidic environmental response dissolving mechanisms. It also aids in preventing dangerous freeze-ups from disrupting the routine operation of HVACR installations.
Manufacturer Requirements
Manufacturer evacuation criteria are critical in guaranteeing the operation and efficiency of HVAC systems. Evacuation is a necessary procedure for removing any moisture, air, or impurities from the system.
Failure to conduct effective evacuation might lead to poor performance and significant damages.
Some manufacturers have more stringent standards than ASHRAE because they want to achieve higher levels of purification during compressor replacement and maintenance activities.
By mandating evacuations as small as 400 microns, all water vapor trapped within the refrigerant circuitry is cleared, leaving no residues behind.
The rigorous regulation is mostly applicable when dealing with high-end equipment like chillers. It necessitates ultra-clean pipelines devoid of moisture buildup, which can drastically impair their performance.
Otherwise, it may have an effect on overall energy usage by increasing it unnecessarily.
Before adopting arbitrary micron ratings, personnel doing repairs or replacements should frequently consult manufacturer documentation. Because each evaporative coil has a varied capacity value and holding capacity depends on the amount of R-22 refrigerant used.
The size/installation elements impacting inside temperatures determine the heating/cooling combination required.
Adhering to manufacturer evacuation ratings is critical to maintaining the proper operation of HVAC devices. It aids in lowering the likelihood of failure due to unintentional installation errors.
If chronic faults persist after warranty claims are denied, the errors may wind up decreasing customer trust in the brand’s reputation. After saying that the lead unit was inexperienced in handling the current circumstances, etc., faults were raised.
After that, people start blaming others instead of taking responsibility and working together to make progress.
Acceptable Micron Rise
Evacuation is a crucial step in installing or servicing refrigeration and air conditioning systems to remove moisture, non-condensable gases, and other contaminants from the system.
An acceptable micron rise indicates the level of vacuum pressure that should be maintained while evacuating the system.
Importance of Evacuation
A good evacuation ensures component dependability owing to equipment dehydration prior to charging. It decreases the possibility of acid development in operational components such as compressors.
It increases energy efficiency by lowering heat resistance caused by damp systems. Finally, it makes a significant contribution to maintaining appropriate indoor air quality.
Micron Levels in Evacuations
When removing moisture from a system during the recommended after-installation evacuation process, ASHRAE suggests pulling vacuum levels below 1000 microns. This can ensure that the system runs smoothly from the outset.
Because compressor failure could have resulted in contamination, ASHRAE additionally recommends a filter size of less than 500 microns after replacing the compressor.
Some manufacturers even propose obtaining an ultimate low-pressure reading of “400” microns on electronic gauges. This proposed threshold would generally operate appropriately, especially if excessive humidity was expected.
Where very little airflow travels through evaporators, causing any relative pressure readings collected at higher pressures to drop over time.
An acceptable micron rise is the amount of pressure increase per minute that often indicates the presence of leaks. (although it may not always rule out possibility.) Ideally, a no-rise condition should be realized with held-for-time intervals associated with naturally larger volumes.
Otherwise, accurately tracking down rises necessitates advanced measuring techniques.
Factors Affecting Acceptable Micron Rise
- Size matters: The total volume used will determine half-life decay; sufficient piping sizes, as well as valve seals, are also required.
- Vapor Pressure: Large volumes (and/or nature) of some oils, together with background water vapour formation, tend to either lengthen overall times or shorten overall periods.
- High humidity areas: Makes maintenance work more difficult, especially when the ambient air quality is severely below standard.
- Access to Equipment: It can also play an important role in accuracy and reliability, especially in older systems where response times may not correlate with established measures.
Examples of Acceptable Micron Rise
Critical applications (e.g., electronic chambers) require a lower micron acceptance level ranging from 2 up to about 10 mm Hg.
Low charge/noncritical service application’s may accept rise above over longer testing periods due less likely impact on performance or compressor/reliability.
An acceptable micron rise denotes an increase in pressure within a specific timeframe during the evacuation process. Vacuum levels achieved during evacuation procedures can be affected by factors such as system size, vapor pressure, and humidity levels.
All of these should be examined on a frequent basis and methodically rectified in order to create efficient return airflow into components. According to several refrigeration equipment manufacturers, arbitrary figures are minimized by recommending the use of sensors such as Digital Vacuum Gauges for real-time readings, which improves detection capability overall.
The importance of performing correct and thorough evacuations assures long-term component operation efficiency. As a result, adding to the perspectives of Indoor Breathing Environments governing agencies.
Risks of Improper Evacuation
Evacuation is an important process in HVAC system maintenance. The purpose of evacuation is to remove unwanted moisture, air, and other contaminants that may be present within the refrigeration circuit or air conditioning system.
Improper evacuation can result in decreased efficiency of equipment which would lead to more energy usage than normal.
After performing preventive maintenance, ASHRAE recommends a vacuum pressure level of less than 1000 microns for optimum moisture removal from the system. Before restarting operation, do maintenance such as filter changes, and shut down the compressor pump.
Due to the possibility of contamination from oil mixing with replacement gas, direct expansion line tapping should be performed initially, followed by direct expansion line tapping until it reaches 400 microns.
However, service technicians must adhere to the standards outlined in the manufacturer’s operational manual. As they require evacuation beyond ASHRE requirements, particularly when installing new systems that necessitate a thorough dry-out process.
Effects on System Performance
Failure to adequately evacuate the AC would result in excess vapor buildup, resulting in a higher head pressure-induced compression ratio rise. It prevents indoor temperature from reaching the target point, posing a safety risk because to the high torque on rotor turbines.
Furthermore, the compressor’s loud valves result in poor cooling/heating performance while consuming excessive amperage. That you are consuming too much electricity, which is causing your energy expenses to skyrocket due to poor thermal comfort.
It has an effect on the health of the occupants over time. Mechanical breakdown is the best-case scenario, while complete shutdown is the worst-case situation. In cases like this, you can choose Atosa brand.
Risks of Moisture and Contaminants in the System
Moisture causes interior corrosion of metals, reducing lifetime expectancy and interfering with optimal heat transfer between hot and cold media. As a result, lowering the unit’s functioning rate raises repair costs and downtime, jeopardizing the customer’s business continuity if used in a commercial application.
Furthermore, some physical, solid, and gaseous contaminants are attracted into pipelines during transportation/manufacturing, among other things. Any manufacturing debris left behind will impede the entire HVAC cycle unless adequate filter driers/moisture indicators are installed.
Furthermore, it is significantly causing costly component replacements, electric motor burnout, and valving issues. Problems such as clogged capillary tubes and limits reduce system life-span.
Long-term Damage to System Components
During the manufacturing process, many impurities such as welding solders, torch residues, and joint flux can cause equipment to malfunction. Unsatisfactory evacuation results in the intrusion of ambient air, which contains used refrigerant and breaks down compressor oil.
As a result, full failure occurs, affecting the entire heating/cooling process. Inadequate lubrication causes friction among bearings/seals, weakening shafts, and lowering inlet valve suction.
The best-case scenario is that capital is wasted, while the worst-case scenario is that uninhabitable spaces result in partial restorations due to damage beyond repair.
Proper evacuation ensures proper functioning order by removing potentially harmful impurities, resulting in a longer lifespan. It is completed with less disruption to business continuity/environmental quality/lower utility costs, making HVAC system maintenance vital for the well-being of all building occupants.
What is an Acceptable Micron Decay Rate?
An acceptable micron decay rate is below 1000 microns. It is considered for R22 system containing mineral oil. The holding time should be long enough to ensure a stabilized vacuum reading.
During the stabilization period, there will be changes in readings over hours or even days.
A finishing vacuum of 500 mcrons is commonly recognized as a realistic aim for most systems. The vacuum level is determined by factors such as the system’s size and construction complexity.
Additional sensors would be recommended for greater suction lines enabling evacuation aided by isolation valves. Before opening the refrigeration circuit, it is critical to record the starting point of any repair work.
Measuring equipment varies based on the application, such as condenser coils, which require a high CFM intake gauge set or core removal tools. A properly working pressure regulator can boost overall efficiency by guaranteeing good cooling throughout evaporator coil regions.
What is the Maximum Micron Rise Allowed for a Leak Free System?
Vacuum Pressure
The vacuum pressure should be brought down to 1000 microns.
Valve Off the Pump
Once the system is evacuated, turn off the valve of pump.
Micron Rise Limit
If after 30 minutes, micron reading doesn’t rise above 2500 it ensures that there are no leaks in the system.
Leak Detection Check
A micron gauge should be used to detect any leakages and ensure the proper functioning of systems
Importance of No Leaks
An airtight and leak-free system ensures efficient operation while avoiding wastage or damage due to malfunctioning parts.
To Recap
While maintaining recommended micron levels after evacuation is necessary to remove harmful water vapor from a refrigeration system, slight increases in microns over time may not necessarily mean inefficiency if managed properly.
Technicians should prioritize regular monitoring and maintenance of their systems to ensure they continue operating at optimal performance levels within acceptable limits.